ammonia fuel handling solutions
Complete ammonia bunkering terminals
Onshore bunkering terminal
The onshore bunkering terminal is a cost-efficient solution within industrial zones and harbours with available land area.
The onshore bunkering solution allows ship bunkering alongside the quay or transfer to a bunkering barge. Large terminals can double as bunker storage terminals for a fleet of bunkering vessels. ‘
The system can receive ammonia from tank-trucks and ships, in compressed, semi-refrigerated or fully refrigerated state.
Floating bunkering terminal
Our floating bunkering solutions are movable and thus ideal for the early years of using as ammonia fuel, when fuel demand is uncertain and likely to develop quickly.
The stationary bunkering barge offers an ideal solution for projects where available land is limited. The barge will be moored or chained to quay and may function as an extension of the quay, reducing the need for quay investments. The barge can be relocated or replaced to respond to local ammonia fuel demand.
bunker vessel
The Azane self-propelled bunkering barge (bunker vessel) suits locations with restricted land space, large bunkering volumes, and a need for operational flexibility. Bunkering and loading will be done ship-to-ship either mid-sea at anchorage or alongside when receiving vessel is at quay, avoiding sailing to dedicated bunkering quays. This is the an ideal solution for vessels requiring large volumes and where bunkering at dedicated quays are challenging.
FLEXIBLE STORAGE OPTIMISED FOR SAFETY.
- Refrigerated storage to minimise safety risk in the event of an ammonia leakage/release
- Refrigerated ammonia offers the highest degree of flexibility with regards to bunkering to vessels with different storage conditions.
NH3 DELIVERY TO TERMINAL FROM ALL SOURCES.
- Truck/Container delivery for our stationary terminals (typically ambient up to 8 barg)
- Vessel delivery ( typically refrigerated ammonia)
- Vapor management system (azaFLEX®) separates impurities and ensures product is kept according to fuel spec.
INTRINSICALLY SAFE DESIGN.
- Storage system and condition of stored ammonia optimised for minimal dispersion
- Transfer system design that minimises human error during offloading/bunkering
- Emergency & Safety philosophy based on decades of LNG bunkering experience and ammonia handling from other applications.
INNOVATIVE BOG HANDLING SYSTEM.
- Decreased energy density relative to carbon fuels requires faster transfer.
- Vapor return and our vapor management system (azaFLEX®) ensures efficient transfer to all fuel tank types without increasing system complexity & cost.
MODULAR & SCALABLE.
- Engineering cost reduced with modular design
- Using same ammonia handling solutions and equipment for our different bunkering solutions
RELIABLE & AVAILABLE.
- Redundancy and spare philosophy optimised for availability and cost
Ammonia handling
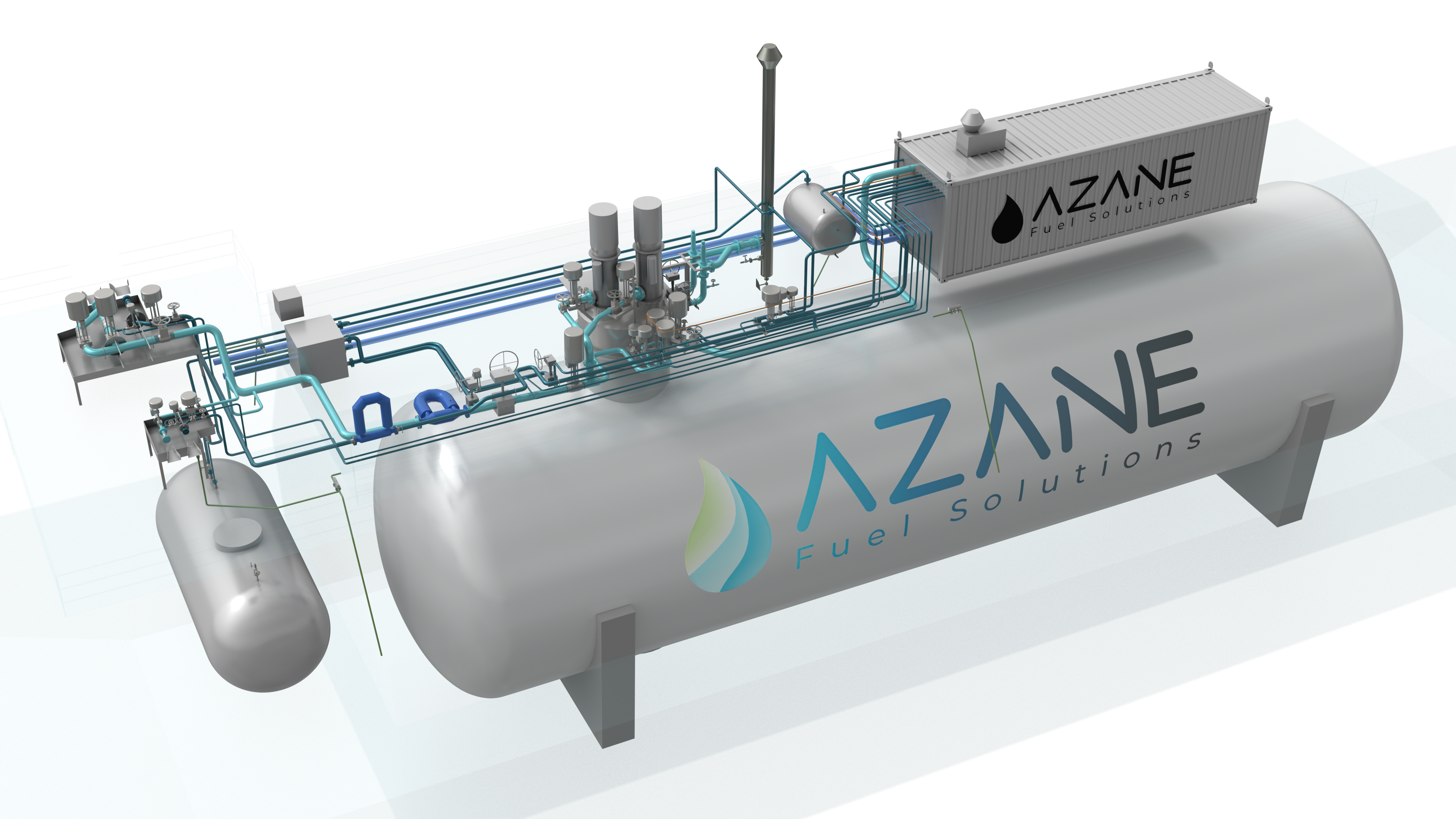
Complete cargo handling system
The Azane ammonia cargo handling system is a complete system for storing and handling refrigerated ammonia as cargo or fuel on bunkering terminals / barges.
The system can be delivered standard for bunkering applications or tailored to other maritime or land applications.
Included modules with Azane cargo handling system:
- azaFLEX® vapor management & reliquefication system
- Control & automation system & separate safety control system
- Complete transfer system including CTS, piping, hoses, couplings
- Ammonia handling system with piping, valves, instrumentation
- Insulated type C storage tank including pump(s)
- Built in ammonia safety systems incl release mitigation system
AMMONIA VAPOR MANAGEMENT AND RELIQUEFICATION SYSTEM
Azane Fuel Solutions proprietary ammonia vapor handling system – azaFLEX®. The azaFLEX system ensures efficient vapor handling, cooling & reliquefication of ammonia – ensuring ammonia is safely stored and delivered as liquid at -33°C.
The azaFLEX system can be used on bunkering terminals requiring vapor management or for other applications such as gas carriers and land applications.
Features:
- Flexible: Built-in flexibility with possibility of several different modes for vapor handling, cooling, and recondensation of ammonia.
- Ammonia as secondary coolant: Cascade cooling function using product (ammonia) as cooling medium – no external coolants/refrigerant needed.
- Separates impurities: Built in separator for non-condensables, removing impurities (mainly O2 and N2) from terminal ammonia handling system. Also enabling vapor return with N2 and O2.
- Easy installation: Skid-based and/or containerized with minimum footprint.
- Enables up to 2x higher bunkering transfer rate with vapor return compared to conventional systems with same compressor capacity.
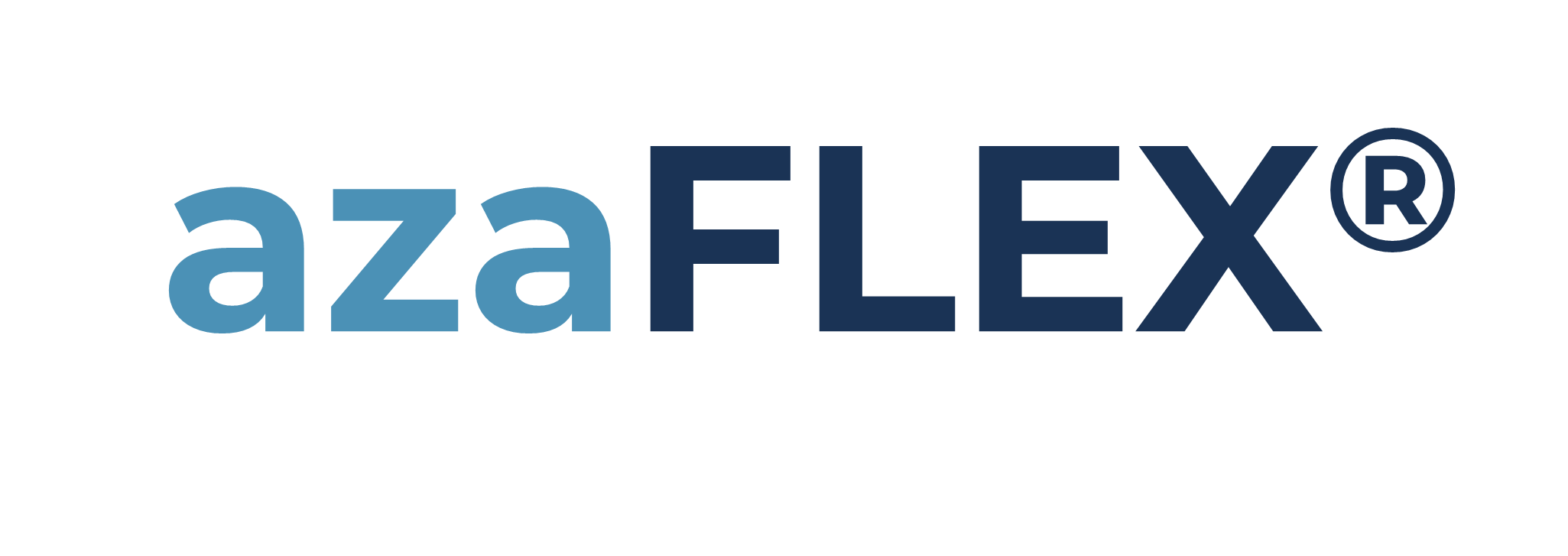
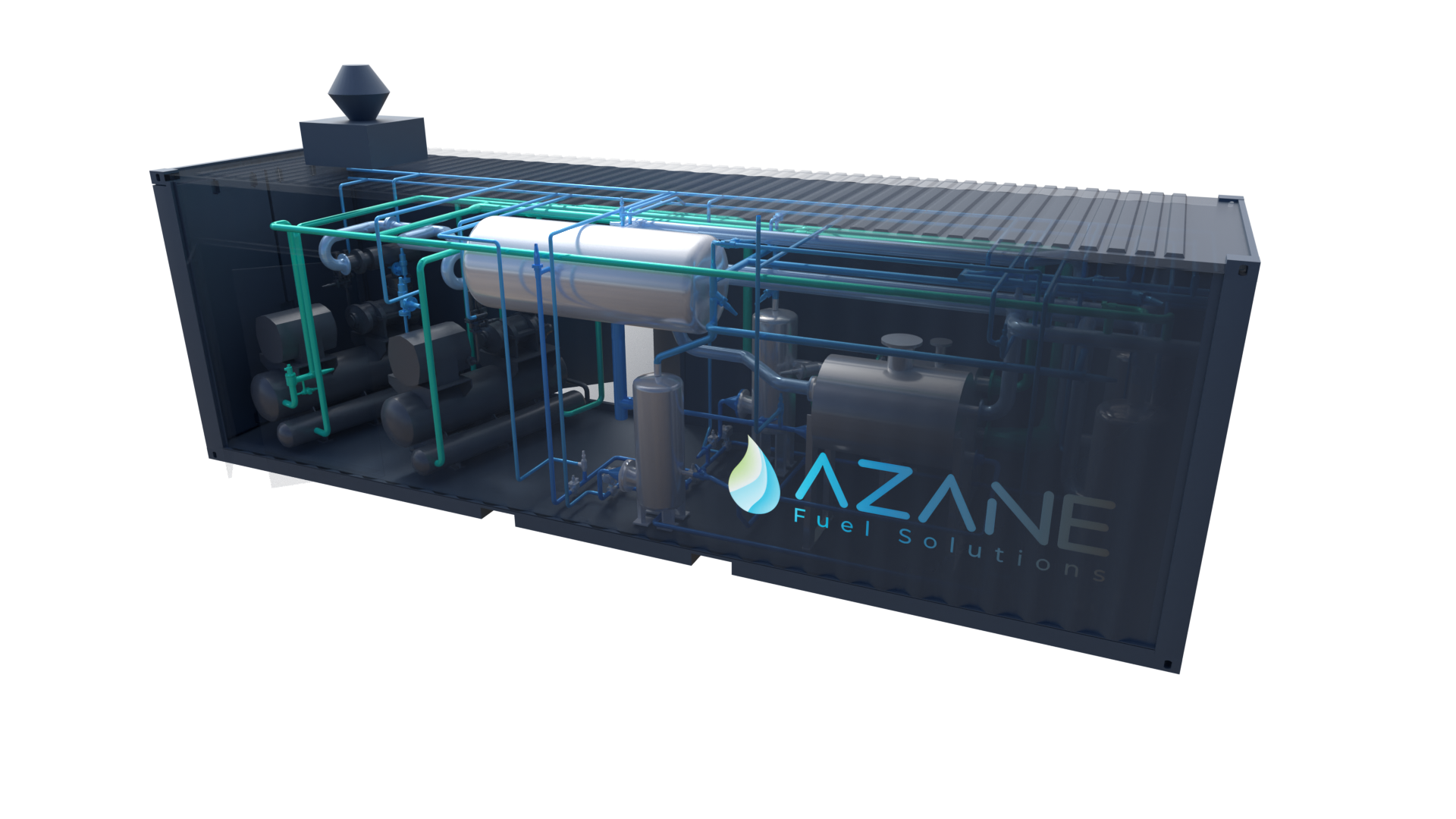
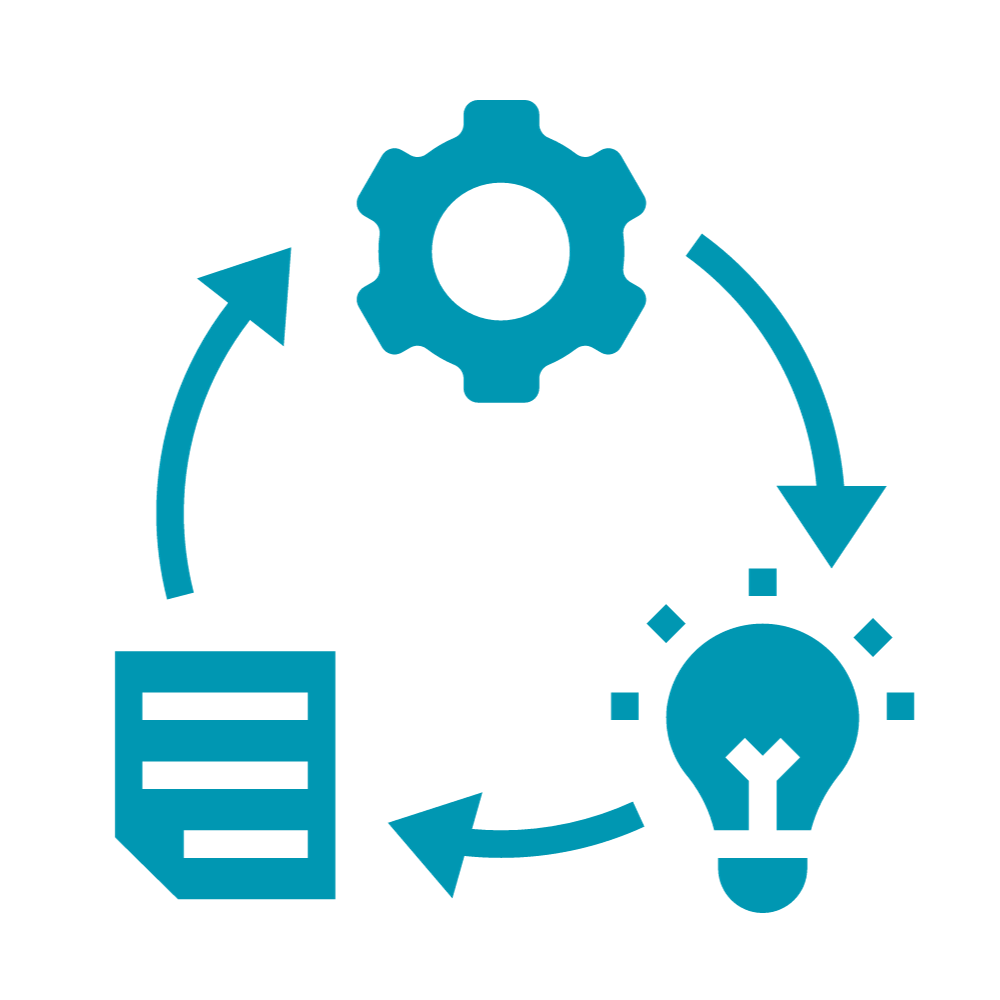
Integrated solutions
Azane offers a range of integrated solutions that can also be delivered as separate products:
- Ammonia cargo heater for applications requiring heating of product before delivery.
- Transfer manifolds with CTS, valves and instrumentation
- Systems for ammonia emissions & release mitigation – ensuring no toxic releases or ammonia odour.
- Ammonia gas detection system
- Other safety systems and equipment for minimizing ammonia leak risk
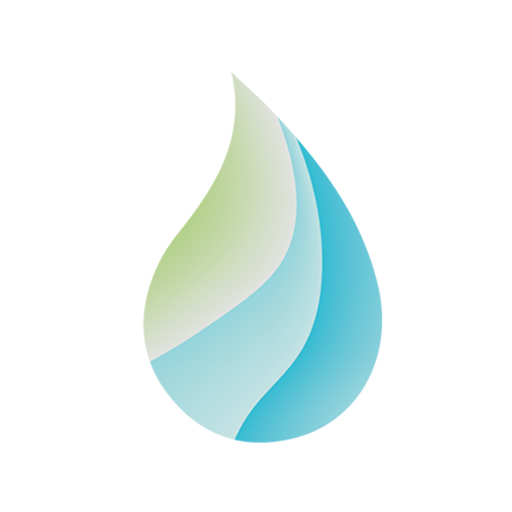
Related services
Our main offering are turn-key deliveries, but we also offer a stepwise service from feasibility study, via engineering & approvals, to construction, installation, T&C and finally start of operations, or alternatively – those services offered separately. For terminals in operation, we offer a wide range of service contracts from full operational execution, to maintenance, condition monitoring and periodical control.
AZANE FUEL SOLUTIONS can provide the following services related to our bunkering solutions:
- Concept and feasibility studies to make an early assessment of feasibility, necessary capacities, and concept selection.
- Location development, concept design & pre-project work including assessment of ammonia fuel logistics and site-specific engineering. This can also include:
- Establishing basis of design.
- Operations preparations and training for terminal owners and operators.
- Organizing relevant safety work such as HAZIDs, HAZOPs and other safety and risk studies.
- Permitting processes including applications and dialogue with relevant authorities and other 3rd parties.
- Full project management responsibility from pre-project to project execution and delivery.

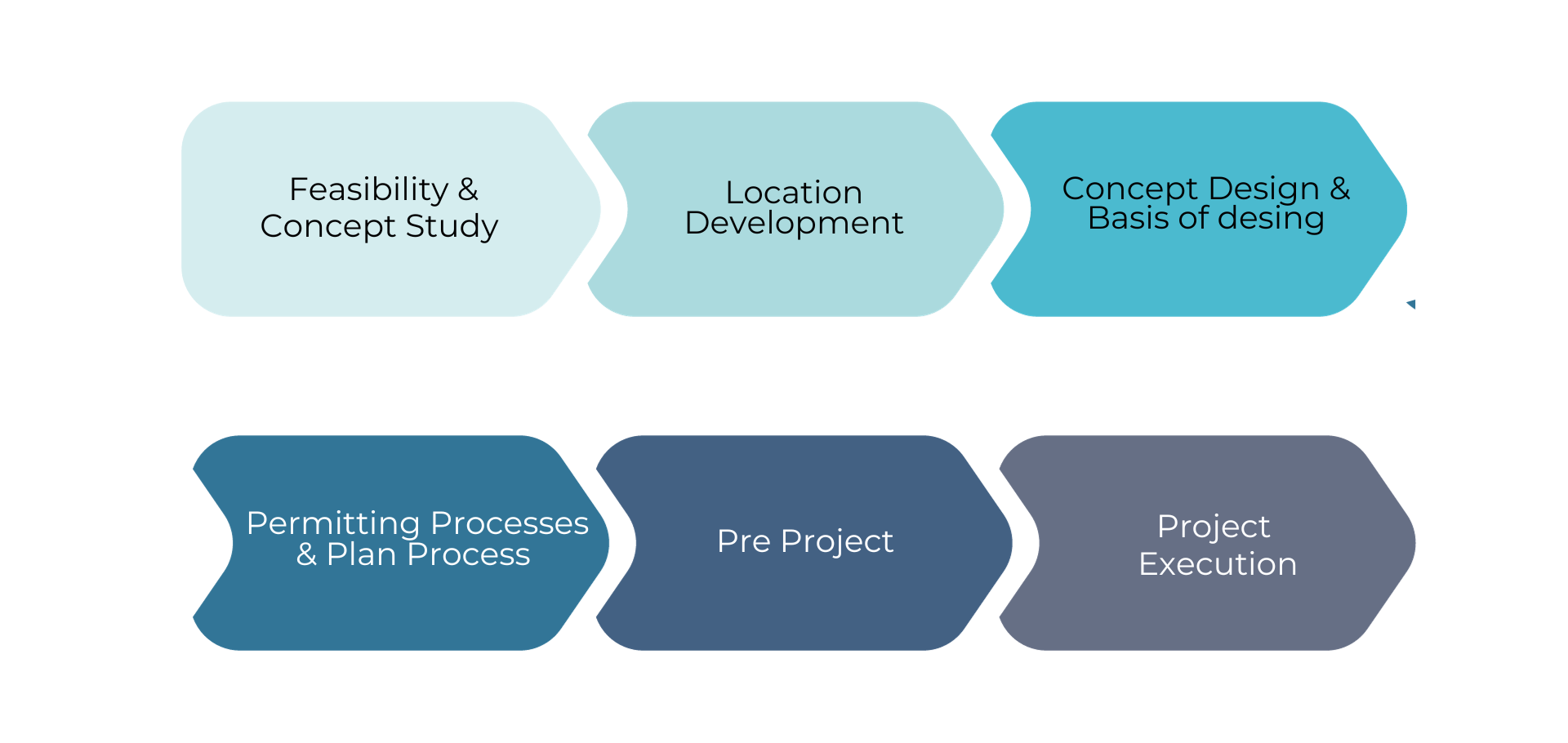